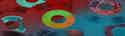
Is it yet another inevitable change in the music business or a long-term threat for independent record labels?
In the first half of 2021, vinyl sales skyrocketed by 94% according to RIAA as recorded music revenue in the US grew by $1.5 Billion (+27%). The growth has mainly been driven by music streaming and premium subscriptions to shops like Spotify, Apple Music, and Deezer, with an increase of 13% compared to the first half of 2020.
Such growth can not only be seen in the US but also overseas in Germany where $1 Billion in revenue was generated from recorded music, a 12.4% growth (Source: Music Business Worldwide).
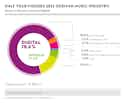
And what happened to vinyl sales? They exploded.
In the US, vinyl sales saw 108% growth during the first half of 2021. As we’re seeing the same in Europe, what’s the issue? People are buying vinyls, so labels and artists should be happy about this, right? Not so fast.
As mentioned by The Guardian, vinyl pressing plants are struggling to meet demand, and well-funded labels are trying to jump the queue. On top of that, there’s a shortage of PVC, which provokes delays from suppliers to the pressing plant, resulting in unusual production delays. A couple of decades ago, we could press records within a few weeks, while today we have to wait between 6 and 12 months. If you’re a record label or an artist with audio and artwork files ready to be sent to the pressing plant, you’ll have to wait almost a year to get your vinyl in your hands. This is not sustainable.
To dive deeper into the factors and consequences of the shortage of vinyl production, we interviewed Mirko Gläser, owner of the German independent label Uncle M Music.
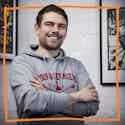
Mirko Gläser, owner of Uncle M
Mirko Gläser is the owner of the hybrid music company Uncle M, based on the German North Sea coast. The company views itself as a mix of a label, marketing/PR agency, music publisher, and consultant for around 75 bands and numerous international labels.
Mirko has been active in the label business since the beginning of the 2000s, and in his earlier years accompanied bands like The Gaslight Anthem, Flogging Molly, Gogol Bordello, Donots, Itchy, and 100 Kilo Herz. Uncle M is connected with iMusician via the band Attic Stories, which publishes its songs in Uncle M's music publishing department Oh Lumiere.
Can you tell us what’s happening with vinyl products and pressing plants?
There are many reasons for what you see happening today with vinyl production. Due to the pandemic, there is a raw material crisis in many industries worldwide. Products based on wood and oil (the main components of vinyl are PVC and paper) are experiencing massive price increases, triggered by huge demand in the construction and manufacturing sector in the USA and China.
The constant closures of Chinese ports due to the local COVID outbreaks have further complicated these matters and have caused immense irritation to the very fragile supply chain and logistics.
In addition, the enormous amounts of energy required for pressing have been costing more and more for several years - not to mention the necessary CO2 compensation. All in all, average manufacturing prices have increased by up to 60% since the beginning of 2021.
There is also another important complicating factor: Vinyl has been booming for several years, and since the end of 2019 it has again become a topic for major record companies, which are now pressing their new releases and also their gigantic back catalogs in ever larger quantities. Around 2010, 700,000 vinyl records were sold in Germany; by 2020, the figure was around 4.2 million and rising.
However, and this is where the problem comes to a head, there are only a small number of German and international pressing plants that can produce such quantities. Apart from a few smaller DIY manufacturers, there are perhaps 3-4 suppliers in Germany who could be called upon for such mass production. Across Europe, there are less than 10.
Vinyl production is a hands-on process - from master creation to mixing special colors. Vinyl fans have become accustomed over the years to getting elaborate color combos (splatter, half/half, egg yolk) and it causes massive delays at these local pressing plants where they are producing vinyl on older machines.
The short form:
Massive competition & fights for the few available pressing slots
Massively rising prices
Disruption of production due to lack of raw materials
How was it before?
Not even 2 years ago, the situation looked quite different. The lead time for the production of an LP (no matter the quantity) took about 6 weeks until the delivery of a test pressing, which is needed for the production release - and after its release, roughly another 6 weeks. Essentially 3 months between the time a band comes out of the studio and the time of a possible delivery of the merchandise to record stores and mail orders.
Nowadays we are talking about 8-10 weeks for the test pressing and at least 6 months for the production of the merchandise.
The threat
The obvious point: today a band would have to submit finished artwork to the pressing plant a few weeks BEFORE their studio date and also already submit detailed information about the planned order (number of pieces, different vinyl colors, etc.). Of course, this is very unusual in the industry, because most bands go "shopping" for the album AFTER their studio date (i.e. offer it to external partners) and roll out the campaign afterward.
It has also become almost impossible to reconcile these crazy lead times with those of booking agencies and clubs, which are also struggling with out-of-control lead times after the pandemic with many venues booked up 12-18 months in advance.
Where this leads to becomes clear at second glance. In the past, newcomers have benefited from the fact that interlocked campaigns can support each other as bands could tour for their album, launch a comprehensive promotional campaign, and generate buzz on a national and regional level. Whereas today, with multiple scheduling delays coming into effect, multiple strenuous attempts must be made to achieve the same goal.
Liquidity also suffers massively under the new conditions. The trend towards advance payment is currently increasing - in other words, more and more studios and pressing plants want to receive payment when orders are placed. These high costs are refinanced by LP sales, which are now up to 12 months in the future instead of 4. In the past, it was easy to bridge this gap with an early pre-sales phase and ensure quick liquidity, but now the risk is increasingly shifted onto the shoulders of the bands and/or their fans. Honestly, what fan of a young newcomer band buys an album 1 year in advance?
For labels, this liquidity pressure is now coming into play. Whereas labels used to give records to pressing plants one after the other and were able to finance the costs of record 2 with the revenues of record 1, they are now forced to pre-finance several (sometimes dozens of) albums simultaneously at increased prices - with uncertain knowledge of delivery and release dates.
The question remains of how these short-term problems will affect the long term. Even without the vinyl crisis, small and medium-sized bands will continue to have massive re-financing problems to recoup studio and pressing costs.
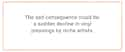
Consequently, a further standardization of albums released on vinyl (chart hits + niche kings) will especially put pressure on specialized record stores and mail orders, which already often face the problem of getting new material into the store at all because of the delay. In any case, the increased raw material and manufacturing prices have led to the fact that an average vinyl album no longer costs 15-20 euros in stores, but rather 25-30 euros. Customers will only buy those albums that they REALLY want. Discovery or random purchases will become less frequent in the future.
One could also ask the question of how many albums a collector can afford as their general wealth and net income have also been affected by the pandemic and general economic crisis.
Many bands are already responding to the current crisis by first releasing albums digitally and then physically three quarters later - which in my opinion will result in additional dramatic drops in sales. Vinyl sales in stores and on tour account for about half of an album's sales (the other 50% usually get sold as pre-orders via their own webshops). If fans can already listen to the album inside and out via Spotify, I have big doubts that the sales at the merch table many months after a digital release will be able to keep up. The consequence of this thought should be to invest even more money in haptics and packaging - but see above: Prices are already exploding for standard pressings. Who can afford even more expensive collector's editions?
If bands and labels aim to continue releasing in sync with the launch of their marketing, touring, and other promotional activities, then they currently have no choice but to stretch their lead times from 6 to 12 to 18 months after recording the album - no matter what the cost.
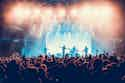
Ready to get your music out there?
Distribute your music to the widest range of streaming platforms and shops worldwide.